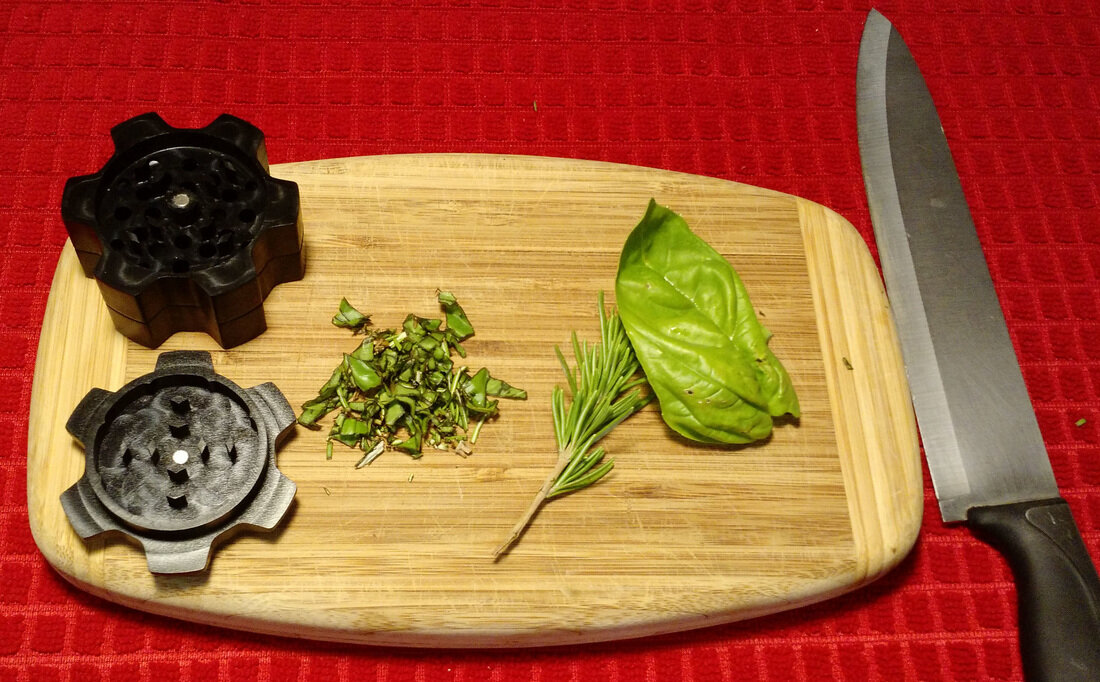
Grinder design for a CNC machining study.
Project Length: 4 weeks
Focus Areas: Product Design, Tolerance Analysis, Fixture Planning, 3D Machining, Type III Anodizing
Materials: 6061 Aluminum, Hard Black Anodize, Neodymium Magnets
For my final CNC machining project at Stanford, I wanted to choose a product that would be challenging in a multitude of areas. A grinder was something that had been on my mind for awhile - its design space seemed well suited for both aesthetics and functionality.
Though the design underwent several iterations, certain features such as teeth patterns and rotational operation were present from early concept sketches. After initial brainstorming, Solidworks proved critical for exploring different form options before actually diving into the internal design. The final gear shape was chosen because of its geometric complexity and to suggest the rotational function.
The grinder is made of three parts each with two unique faces, making CAM programming a complex process. Each piece required a part flip during machining and the misalignment risk here drove the order of operations. In addition, tool lengths and diameters dictated the size of the tooth-and-notch design and the geometry of the storage compartment.
After both sides of the parts had been cut, they were removed from stock, hand sanded, and sent out for hard anodizing - the critical step which would protect and color the aluminum, and make it food safe. The final operation was installing magnets in each part to hold the grinder together when not in use.
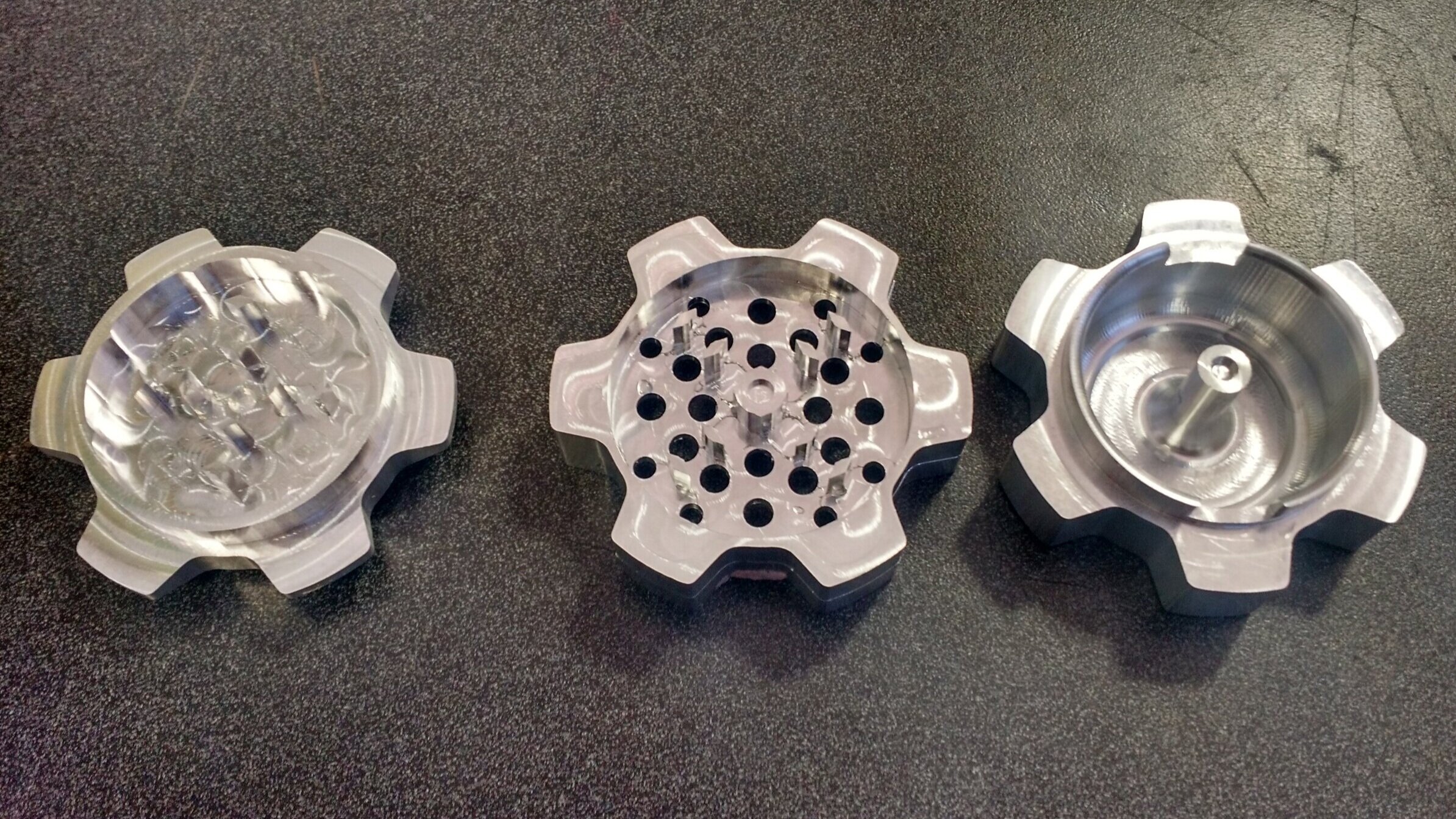
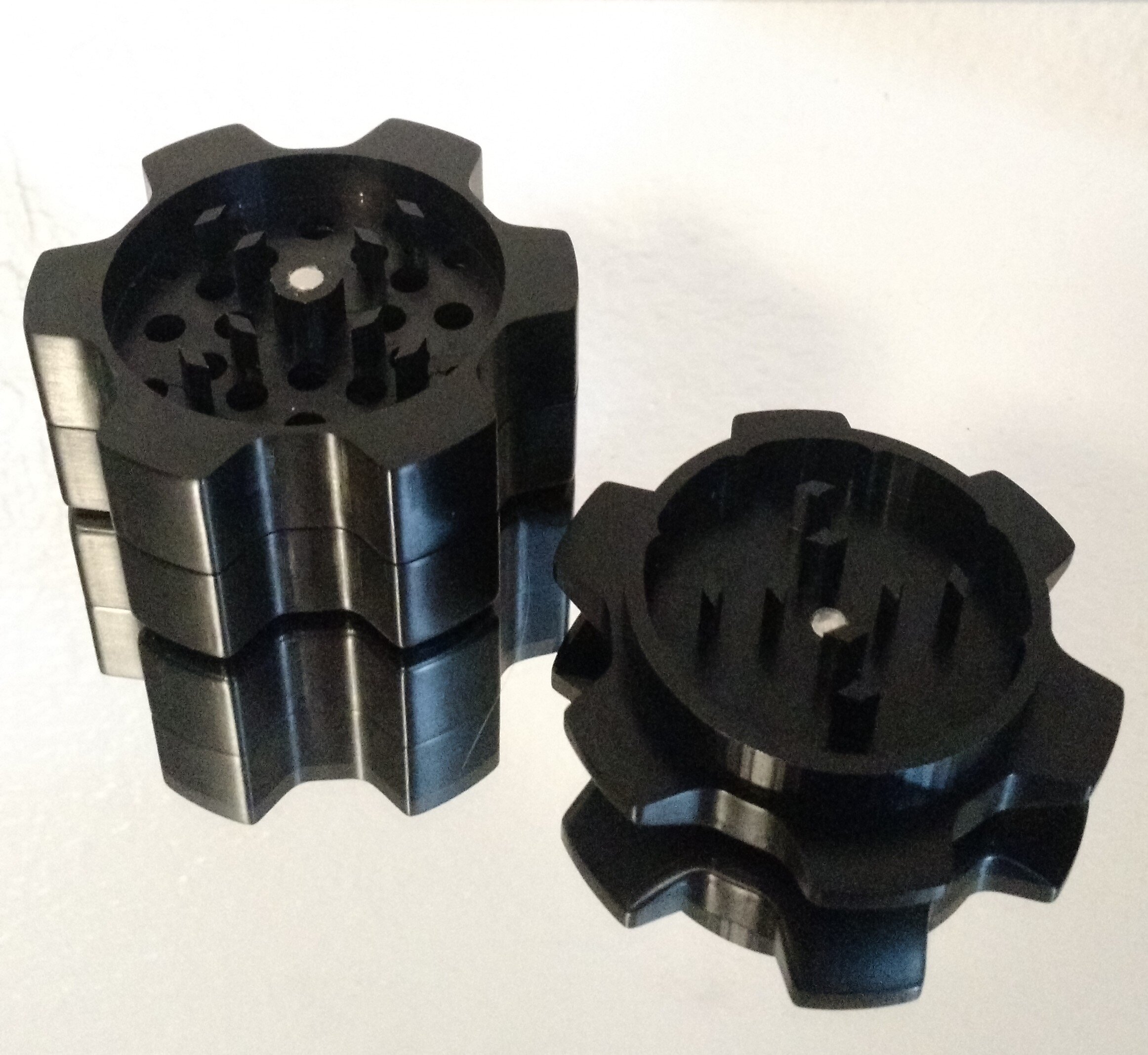

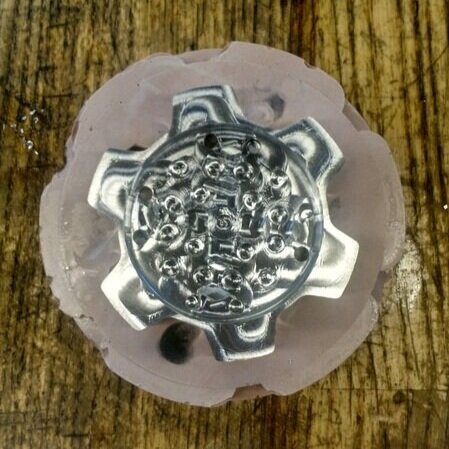
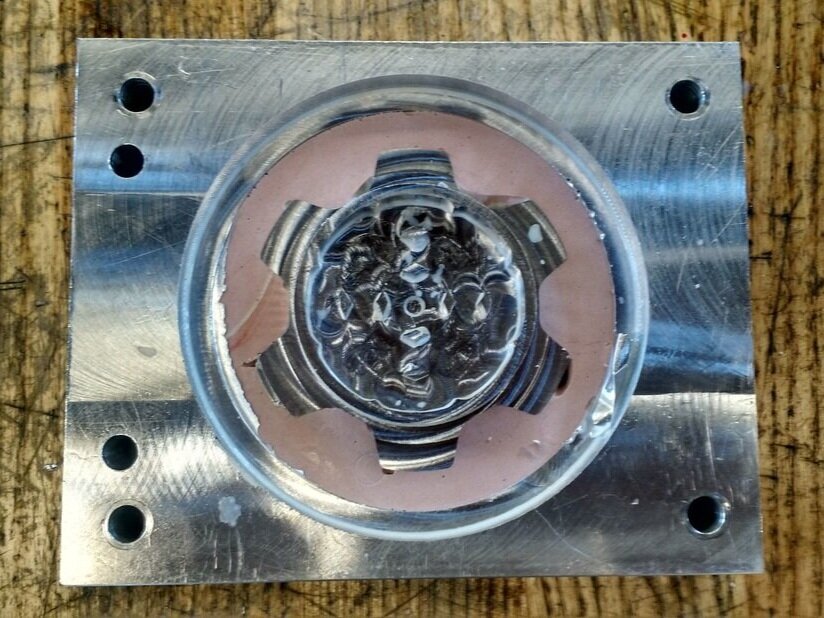
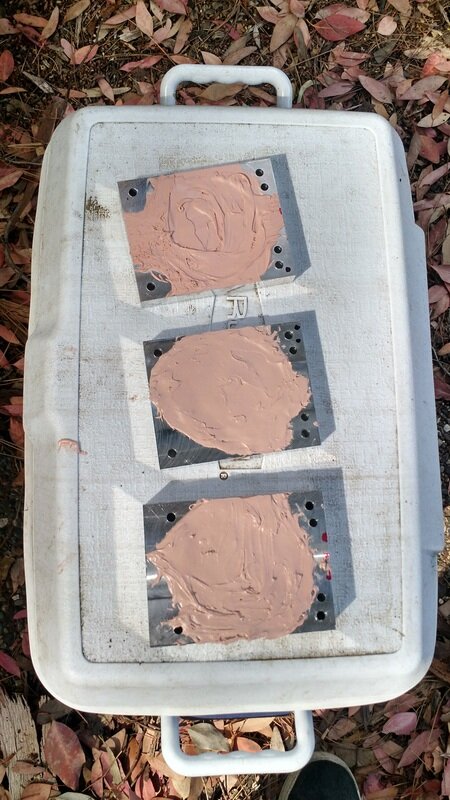
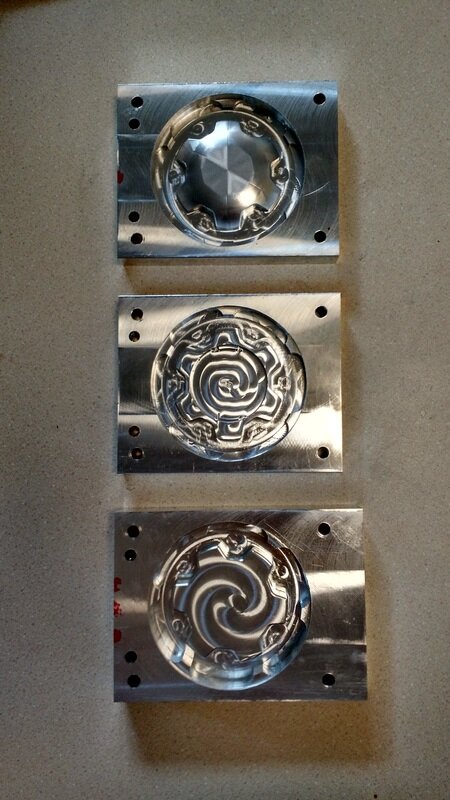
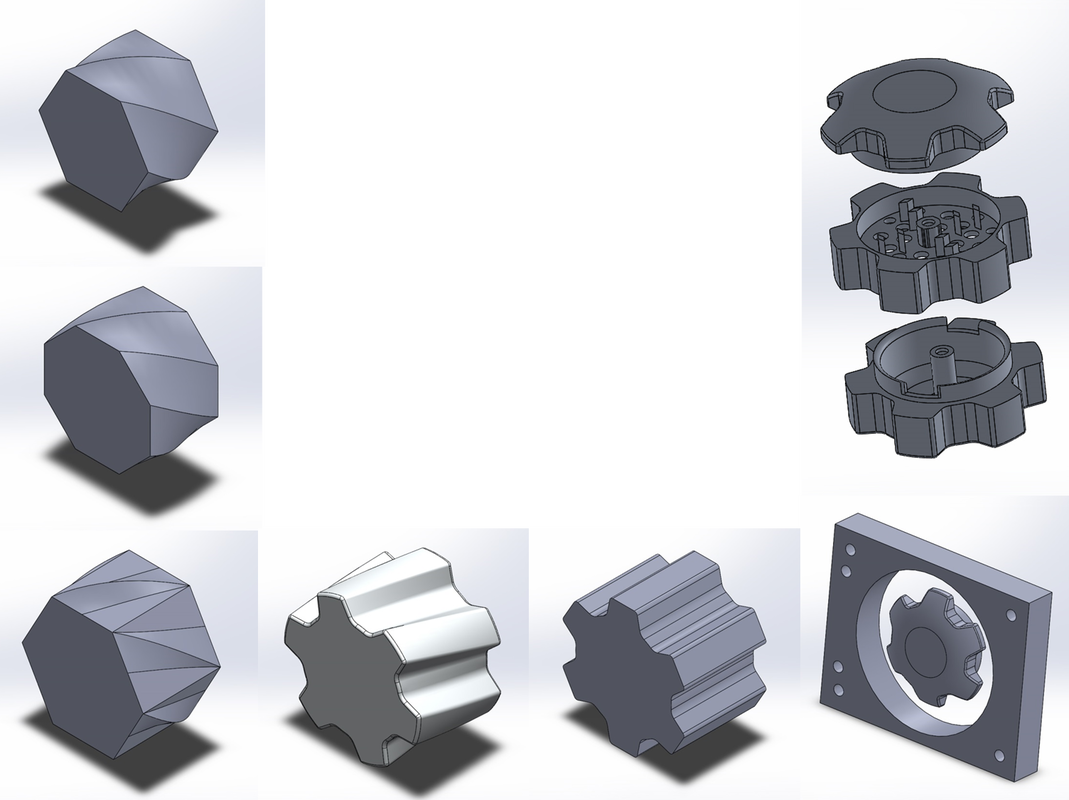
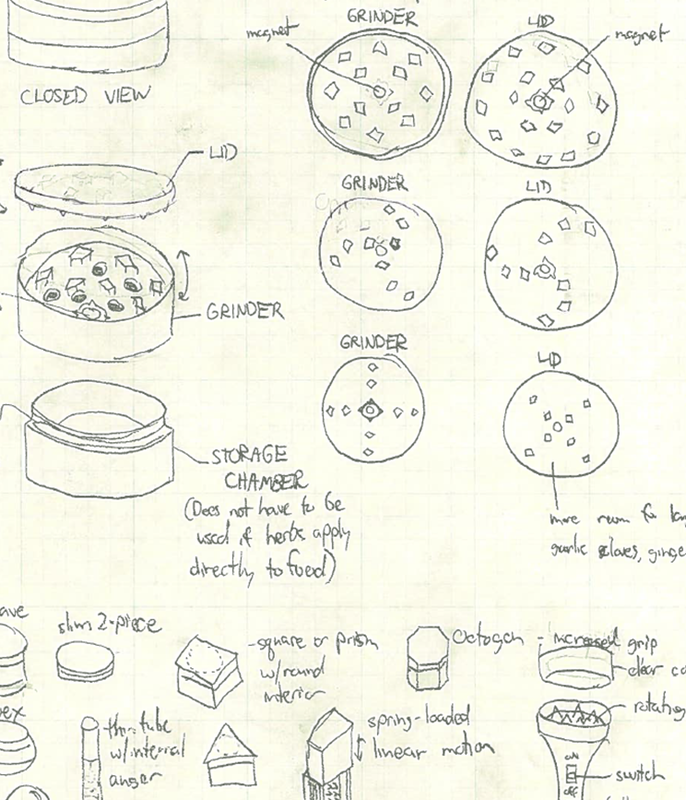