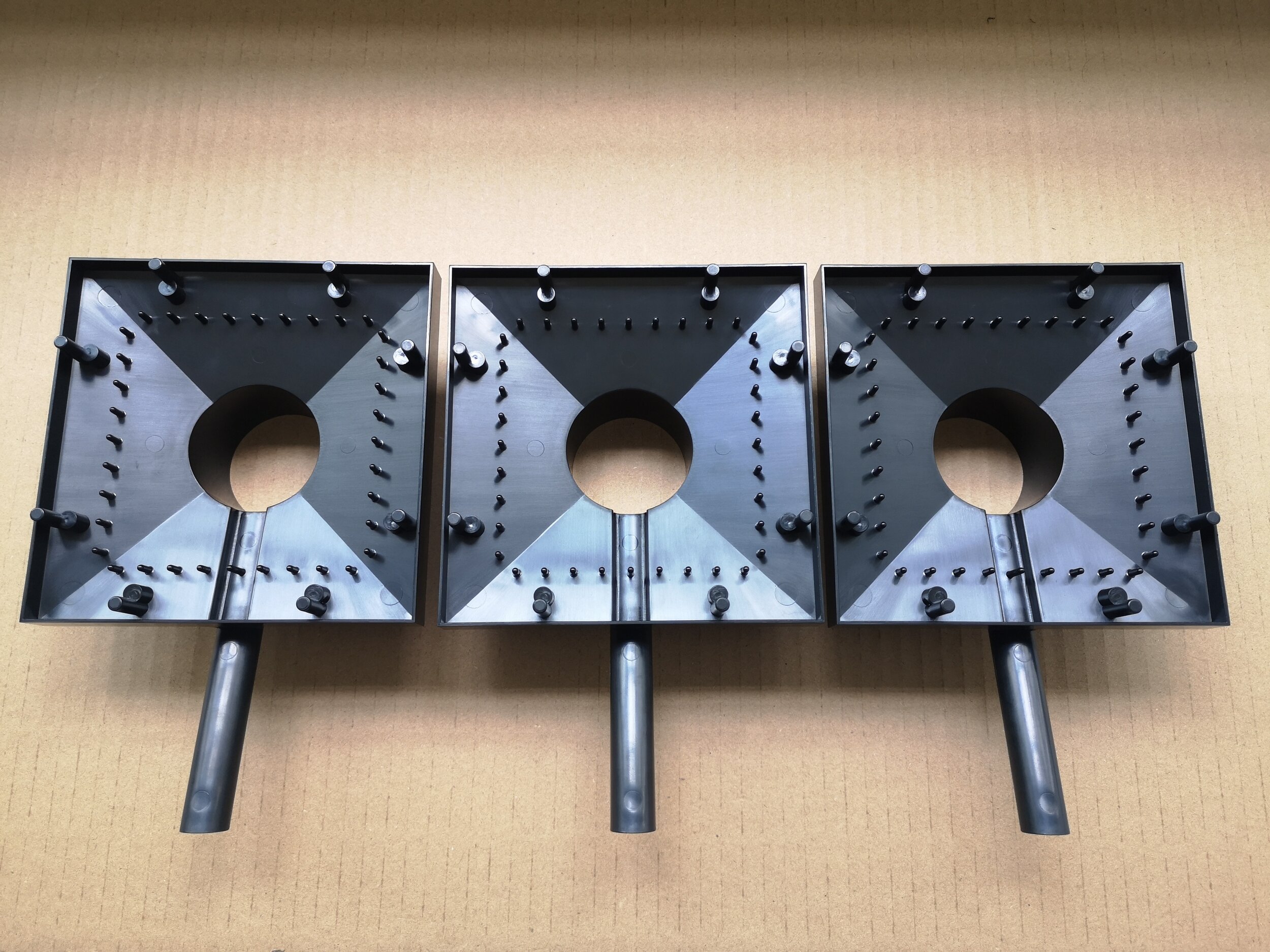
Injection molding optimization via conformally-cooled tool design.
Project Length: 4 week average
Focus Areas: Conformal Cooling Design, Thermal Analysis, Metal 3D Printing, Injection Molding
Materials: ABS, Steel
This work was part of an engagement with Instaversal, a company targeting manufacturing inefficiencies in the Plastic Injection Molding space. The aim was to increase ROI for injection molding projects by optimizing the cooling performance of new and existing tools.
By leveraging metal 3D printing, tool inserts are fabricated with fully-integrated cooling channels consisting of complex geometries and paths previously impossible to produce by traditional gun-drilling techniques. This novel approach allows for faster and more uniform cooling, especially on large and intricate parts. Optimized cooling drastically reduces part warpage, and has yielded a 70% average reduction in cooling time for projects completed so far.
My role for these projects was lead engineer and designer, and my responsibilities include:
Qualification of new projects for conformal-cooling design
Design & modeling of conformal inserts for qualified parts
Manufacturing service optimization
Vendor management & part procurement
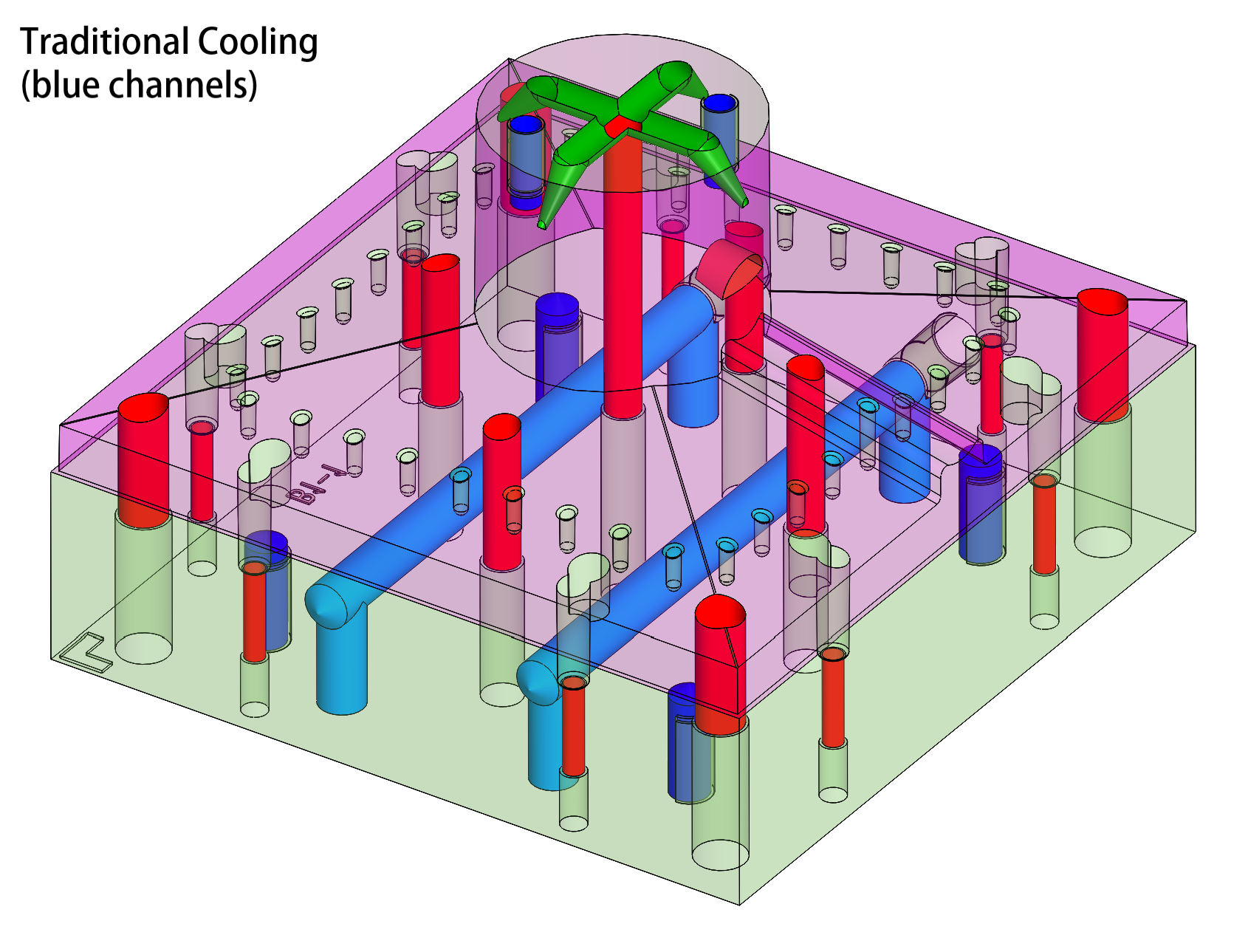
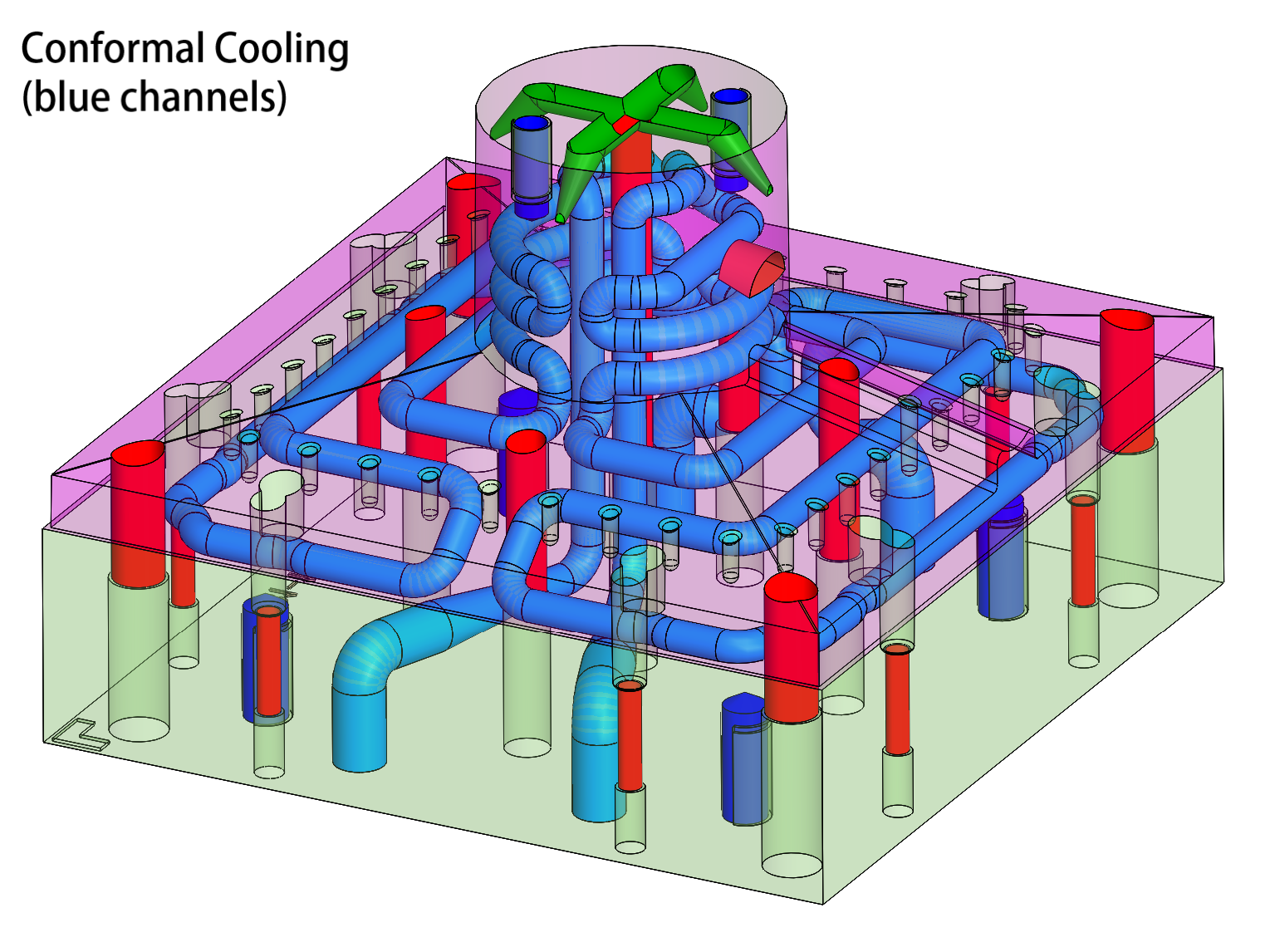



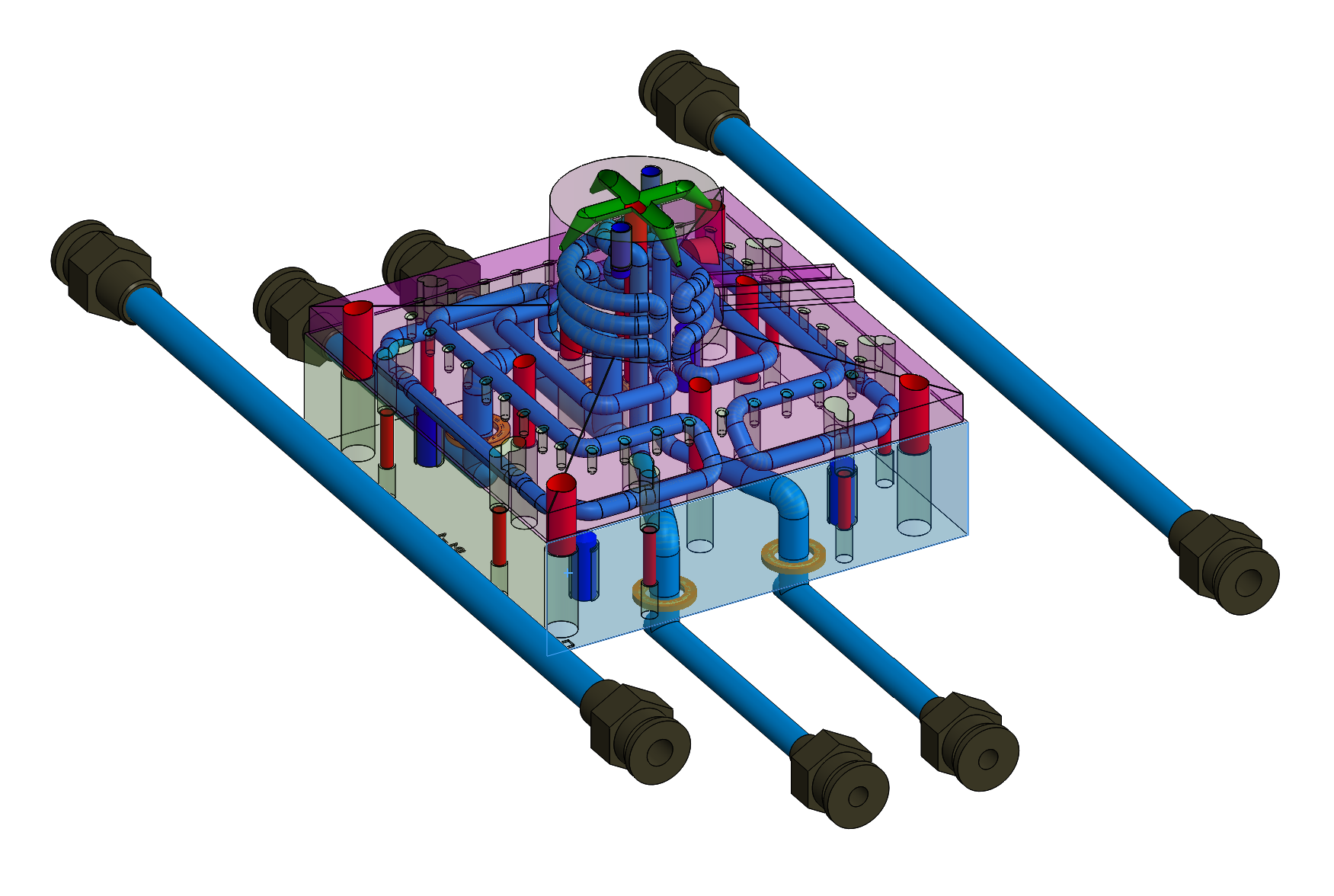
